在
低温四氟垫的生产过程中,厚度控制是一项至关重要的环节,它直接关系到产品的密封性能、使用效果以及适用范围等多方面因素,以下是对其厚度控制的详细解析。
1.原料准备阶段的把控
原料的选择与处理对于四氟垫的厚度控制起着基础性作用。四氟材料本身的纯度、粒度等特性会影响后续的成型及厚度表现。高品质且粒度均匀的聚四氟乙烯树脂原料,在后续加工时更易于均匀受压、分布,有助于形成厚度较为一致的垫片。在配料环节,要精准按照生产工艺要求确定各原料成分的比例,避免因原料比例不当导致材料在成型过程中出现密度不均,进而影响最终的厚度。
2.成型工艺中的关键操作
在成型工艺里,无论是模压成型还是等静压成型等方式,对厚度的控制都有严格要求。以模压成型为例,模具的设计精度是关键因素之一。模具型腔的尺寸公差需要严格控制在极小范围内,其深度直接决定了低温四氟垫的初始厚度设定。在压制过程中,压力的大小、施压时间以及施压的均匀程度同样不容忽视。压力过大可能导致材料过度压缩,使垫片厚度偏薄;压力过小则可能无法使材料充分压实,厚度超出预期范围,且还会影响其密度和密封性能。同时,施压时间要恰到好处,保证材料能稳定成型,而均匀施压才能避免垫片出现局部厚度不一致的情况,确保整个垫片厚度均匀,符合标准要求。
3.后加工环节的调整
成型后的四氟垫可能还需要经过一些后加工操作,比如切割、打磨等,这些过程同样会对厚度产生影响。在切割时,刀具的锋利程度、切割的速度以及进给量等都会影响切割后的垫片厚度精度。使用锋利的刀具且以合适的速度和进给量进行切割,能使切口平整,减少对垫片厚度的额外误差影响。而对于需要打磨的情况,打磨的力度、角度以及打磨时间等都要谨慎把控,防止因过度打磨造成厚度减小过多,破坏产品原本设定好的厚度规格。
4.检测与反馈机制的重要性
整个生产过程中,需要建立完善的厚度检测机制,运用高精度的测量工具,如千分尺等,对生产过程中的半成品以及成品进行定期、多次的厚度检测。一旦发现厚度偏差超出允许范围,要及时反馈给相应的生产环节,调整工艺参数或者操作方法,形成一个有效的闭环控制,确保每一片低温四氟垫的厚度都能精准地达到预定的标准,满足不同低温工况下对密封的严格要求。
低温四氟垫生产时的厚度控制是一个系统且精细的过程,涉及多个环节的协同配合与精准把控,只有这样才能生产出高质量、厚度合格的产品。
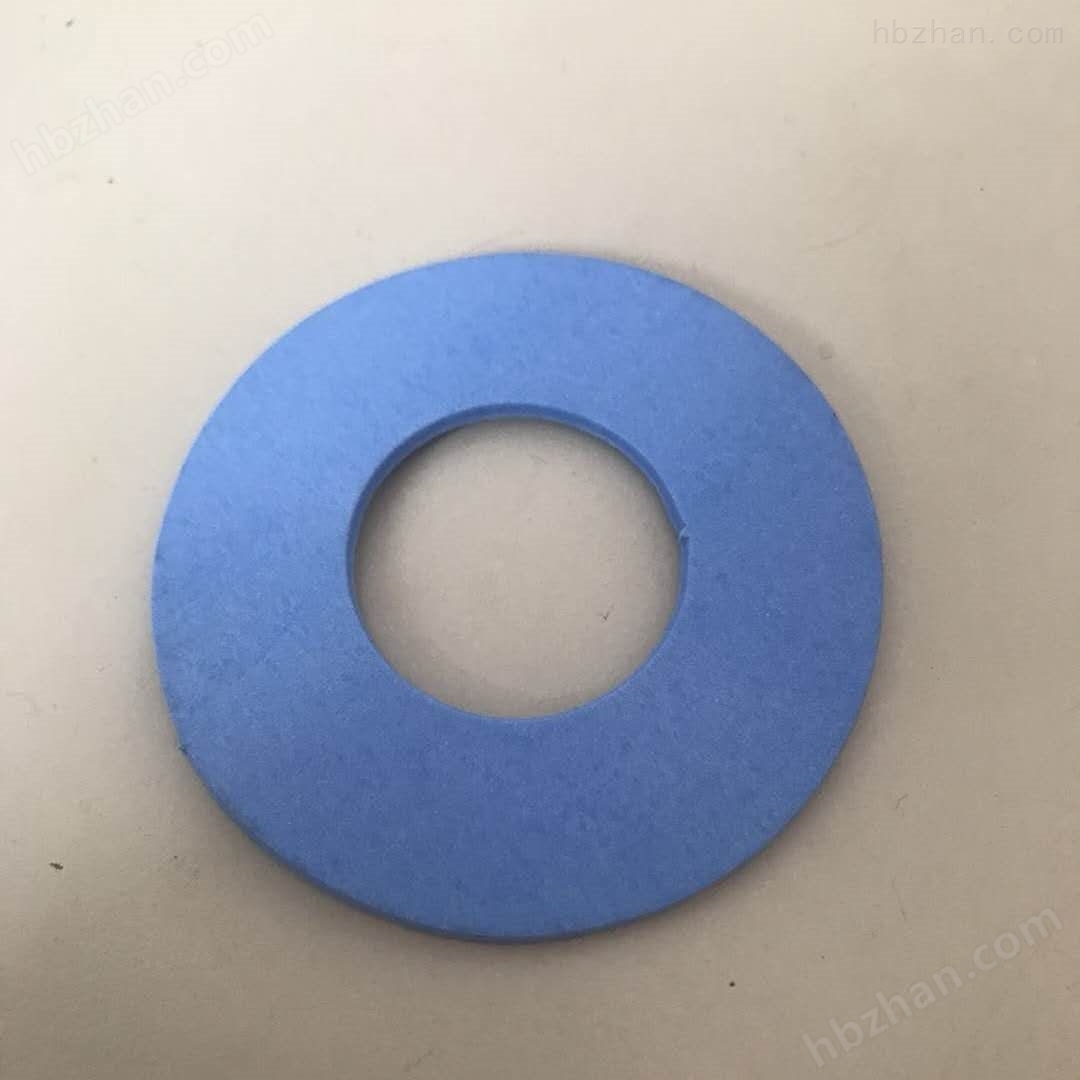